|
| | Fujitsu Siemens Computers Service Logistics |
Service Logistics offers our service partners competent support for the entire IT spare part supply: procurement – planning – inventory management – warehousing – transport management – returns management – repair management – warranty handling. |
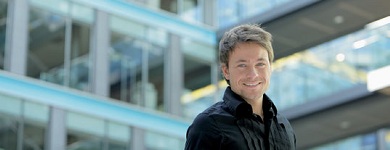 |
Fujitsu Siemens Computers Service Logistics is responsible for controlling the entire spare part cycle - all done on a worldwide, environmentally friendly basis. In addition to the complete range of Fujitsu Siemens Computers spare part components, the spare part portfolio also includes spare parts from well-known IT manufacturers. We continually stock more than 40,000 articles in Germany and in our European warehouses. We currently supply more than 8,000 service engineers and 2,000 service partners in more than 70 countries worldwide. More than 10,000 orders (one or several spare parts) leave our world distribution centers everyday. These figures impressively illustrate our high-performance logistic service which you also can use to achieve your own business objectives. The logistic applications which we have developed have been created as a result of the experience we have gathered in many years of project work and which have been established in co-operation with our service partners. These applications make our services very productive. Such services are available to our service partners 24 hours a day in all our offices within our worldwide infrastructure. |
|
Service logistics packages | 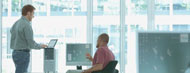 |
A perfect service logistics comprises numerous services. This is why we offer individual service modules supported by our state-of-the-art SAP R/3-based web solutions. |
|
|
Spare parts delivery | 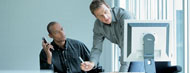 |
Spare parts are delivered from our World Distribution Centers in Ginsheim-Gustavsburg (near Frankfurt / Main) and Sömmerda (Thuringia). We also deliver spare parts from 17 |
regional depots in Germany and more than 300 depots worldwide. The effectiveness and flexibility of our logistic applications optimizes warehouse procedures, such as having various storing/removing strategies, automated label printing and variable order allocation for workplaces. This enables us to adapt each process according to customer requirements. |
| |
|
 |  |  |  |